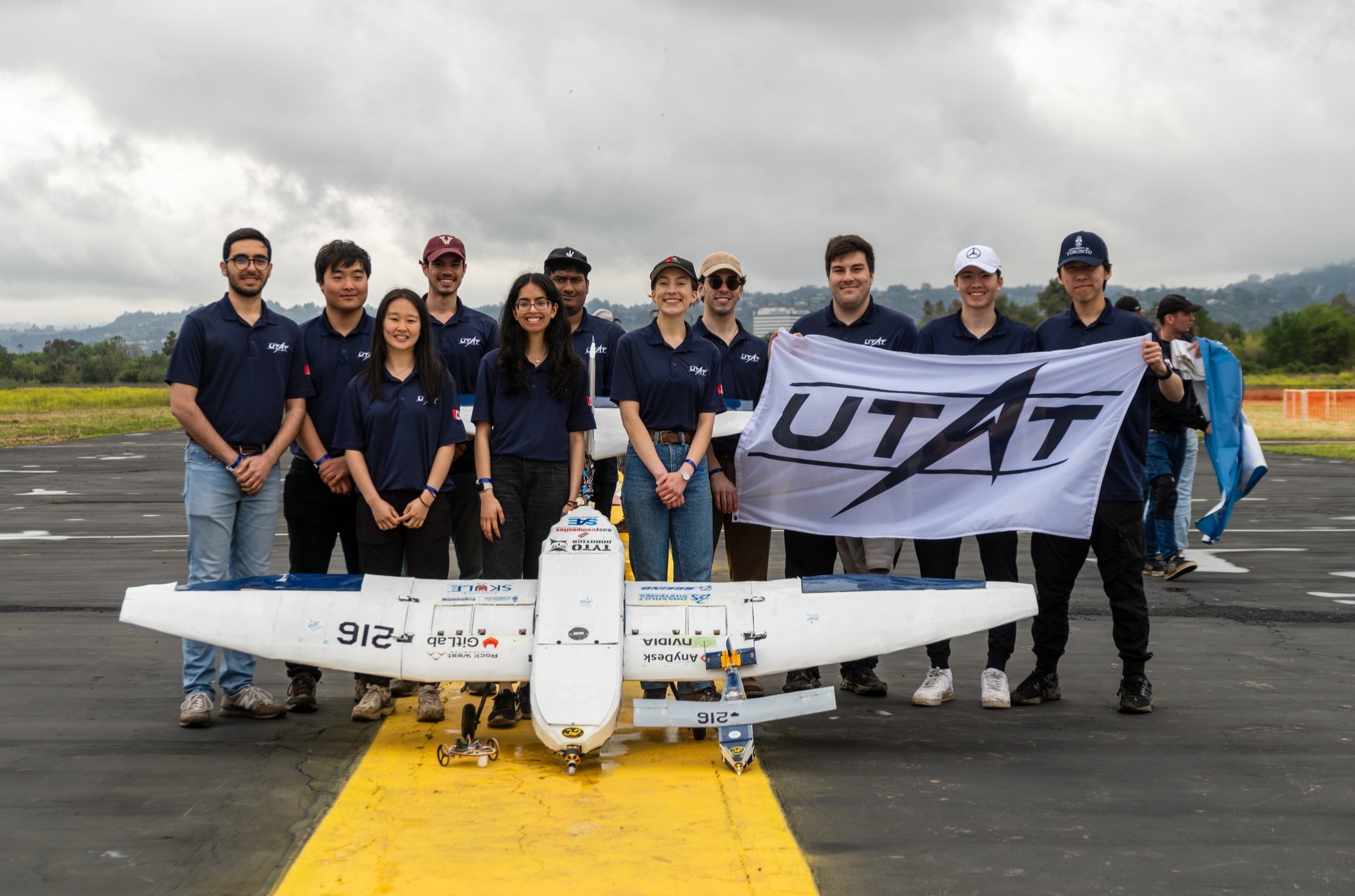
Unmanned Aerial Systems
The Unmanned Aerial Systems (UAS) division designs, builds, and flies remotely piloted fixed-wing and multi-rotor drones. The division consists of two teams: Aerial Evolution Association of Canada (AEAC) and SAE Aero Design.
Due to the multidisciplinary challenges of our missions, we value teamwork, communication, resourcefulness, self-initiative and persistence. UAS is proud to uphold an inclusive culture where all students can develop their technical skills and leadership abilities.
Teams and Subteams
Flight Operations
The Flight Operations team is responsible for the development of flight strategies, mission planning and risk analysis to ensure successful operations during the competition. We are directly involved in the actual flight of the aircraft and the management of all the operational tasks on-site. Throughout the year, the team works closely with other subsystems to organize test flights through which we try to optimize the flight process and improve its efficiency.
In addition, the Flight-Ops team is also responsible for ensuring a safe operation in compliance with the Canadian UAV/RPAS regulatory framework. Examples of tasks include training members to obtain pilot licenses, registering our UAV in the government portal, and obtaining the Manufacturer’s Safety Assurance Declaration for our drones to fly legally in controlled airspace.
AEAC
The AEAC subteam of UAS is focused on competing for the Aerial Evolution Association of Canada (AEAC) Student UAS competition held annually in May in Alma, Québec. Aerial Evolution Association of Canada / Association pour l’Évolution Aérienne du Canada (formerly Unmanned Systems Canada / Systèmes Télécommandés Canada USC-STC) is led by representatives of entrepreneurs, businesses, industry, and government organizations working in the aerial, remotely piloted and unmanned vehicle systems sector. The competition includes executing autonomous tasks using a flying vehicle with mechanical, software, and electrical challenges. This subteam mostly consists of undergraduate students. Each year, students design, manufacture, and test an autonomous multirotor from scratch.
Team photo with UT Cyclone II at the AEAC 2024 competition
UT Cyclone II design
Sub-systems
Airframe: The airframe subsystem designs and manufactures the frame of the drone: the physical base on which the other subsystems are built. Airframe members design and manufacture a drone by analyzing stresses, calculating masses, using CAD (SolidWorks, ANSYS), 3D-printing components, performing carbon fibre layups, and using machine tools to make custom parts.
Mechanical: The mechanical subsystem focuses on the drone’s robotic systems needed to complete the competition objectives. This subsystem works closely with the airframe, electrical, and software subteams to design and build systems such as an unmanned ground vehicle with a garage, or a robotic arm with a gripping mechanism used to transport packages.
Electrical: The electrical subsystem is vital to giving power, control and communication to the drone. This subteam tests and integrates electrical components like the flight controller, batteries, compass, lidar, electronic speed controllers (ESCs), transmitters and receivers. Members gain hands-on experience with soldering, RF link design, cable management, actuation, and propulsion selection.
Software: The software subteam is responsible for making programs for tasks involving computer vision, automated data processing, interoperability, navigation, or path planning. Depending on the competition requirements, specific software is needed to give the drone instructions to make it autonomous.
Flight Dynamics: The flight dynamics subsystem deals with getting the drone off the ground and keeping it in the air safely. This involves PID tuning for the drone using software-in-the-loop simulations and physical test data, managing the drone’s communication systems, and planning flight tests.
UT Cyclone in flight
SAE
The SAE team designs and builds an electric, autonomous aircraft for the SAE Aero Design (Advanced Class) competition. Imitating a package delivery and capture mission, the objective is to design and build a hybrid V/STOL aircraft that takes off conventionally, but transitions to vertical flight to deliver and retrieve payloads. Since teams earn more points for each additional payload weight delivered, the competition focuses heavily on optimization and R&D to achieve the best performance within the constraints. Our membership ranges from first-year undergrad to PhD students, and each year we carry out a clean-sheet design and construction of our competition aircraft!
UT-24 Minerva sharing the skies at competition
The SAE competition team with UT-25 STRATUS
Sub-systems
Aerodynamics: Lifting a heavy payload requires designing an efficient wing, which is the primary goal of the Aerodynamics subteam. Analyses are conducted using a variety of in-house and commercial codes, and the resulting performance is validated in test flights.
Projects: Performance estimation, aerodynamic modelling, shape optimization, wing CAD and manufacturing
Software: The Software subteam is responsible for programming the systems that enable the aircraft to complete its mission with precision and robustness. Various open-source tools used in aerospace and robotics industries are employed and modified to suit our goals and requirements.
Projects: Flight simulation and control, mission planning and execution, computer vision
Electrical: The selection and integration of complex sensors and computers on our vehicles is the primary role of the Electrical subteam. The tradeoffs of size, weight, and power must be balanced, including other constraints unique to aircraft design.
Projects: Motor-propeller matching, sensor selection, circuit design and integration
Flight Dynamics: A plane cannot fly, let alone complete a complex mission, without careful consideration for its stability and control characteristics. The Flight Dynamics subteam achieves this using a variety of simulation models which must be validated in test flights.
Projects: Stability analysis, mass estimation and balance, test flight characterization, empennage CAD and manufacturing
Structures: Extreme weight savings are especially beneficial in aircraft design. The Structures subteam utilizes a host of numerical models and lightweight materials to design an impressively light airframe.
Projects: Structural sizing and optimization, FEA, composite layups, fuselage CAD and manufacturing
Project Overview
UT-24 Minerva
UT-24 Minerva represented an iterative improvement over its predecessor while retaining the same overall configuration. Changes to the preliminary design algorithms and a proactive approach to reducing the part count led to improved performance, weight reduction, and streamlined manufacturing for the team. Thanks to these efforts, the team was awarded 1st place in the design report for Minerva.
UT Cyclone II
Cyclone II is an improved version of UT Cyclone designed to carry a passenger payload over a similar distance as Cyclone I, with increased reliability for the 2024 AEAC competition. Cyclone II features a more aerodynamic and safer cabin, and incorporates design elements planned but not implemented for Cyclone. With Cyclone II, the AEAC team scored 1st in the on-site presentation.
UT Cyclone II
UT Cyclone
Cyclone is a hexacopter in a spiral configuration designed to carry a 2 kg simulated passenger payload over 10 km for the 2023 AEAC competition. At competition, its total mass was 14 kg, and its width from motor-to-motor was 1.5 m. Cyclone was designed from scratch and flown in under six months. With this UAS, the AEAC team scored 2nd in the competition design paper and 3rd in the on-site presentation.
UT Cyclone in action
UT-23 SMOKEY
SMOKEY (or, the Standoff Multistage Operation for Kinetic EntrY), named after the esteemed wildfire awareness mascot, was our challenger to the 2023 SAE Aero Design West competition. Its balsa and carbon-fibre construction came about after many rounds of optimization, allowing it to carry more than its own weight in water payload.
UT-23 SMOKEY in action
UT-22 TEMPEST
TEMPEST (Transport and Ejection of Mounted PADA Ensuing from Site Targeting) was designed to rain down on wildfires for the 2022 SAE Aero Design East competition. An enormous wing enabled a strategy of maximizing takeoff weight by lumbering slowly across the sky, which also aided the site targeting objective.
UT Vanguard
An X-frame quadrotor featuring a garage carrying an unmanned ground vehicle. Designed for delivery of medical supplies. Competed in Unmanned Systems Canada 2021, where it won the design paper phase and placed 2nd in the flight phase
UT BlackHawk
Teardrop-shaped quadrotor designed for surveillance tasks and featuring a custom carbon fiber frame. Competed in Unmanned Systems Canada 2018-19 (UTAT Aerial Robotics).
UT Explorer (UTX)
Conventional fixed-wing aircraft designed for autonomous navigation and airdrop capabilities. Competed in AUVSI SUAS 2017-18 and won the flight portion of Unmanned Systems Canada 2017 (UTAT UAV).
UT Whirlybird
Compact quadrotor designed to deliver a roll of toilet paper to a camper. Plywood-foam core sandwich panel construction. Competed in the Unmanned Systems Canada 2016 (UTAT Aerial Robotics).
Blue Archer
Conventional mid-high-wing, tractor aircraft designed for minimum empty weight and accurate airdrop capability. Competed in SAE Aero Design Advanced Class 2013-15 (UTAT Powered Flight).
UT-25 Stratus
UT-25 Stratus was designed in response to a major mission overhaul for the 2025 SAE Aero Design season. New requirements limited the aircraft to 3.5lb (1.59kg), while incorporating new autonomous and V/STOL capabilities. The fixed-wing tricopter design incorporated more rigorous preliminary design analyses and an advanced software and hardware set-up to autonomously locate and land within 10cm of its payload.
History
UTAT UAS was formed in September 2019 through a merger of the Aerial Robotics and UAV divisions of UTAT. While initially Aerial Robotics and UAV split their domains along the multirotor/fixed-wing aircraft dichotomy, eventually both divisions came to work on similar projects (and even competed against each other at the Unmanned Systems Canada design competition!). At this point, it was decided to merge the teams to better share the knowledge and resources between all members.
UAS team history can be traced all the way back to the Powered Flight division, which was active between 2006-2015. Powered Flight designed and flew gas-powered RC airplanes for the SAE Aero Design student competition.
Achievements
Notable achievements of UTAT UAS
SAE Aero Design East 2025 (Advanced Class): 1st place Design Report and 5th overall
Location: Fort Worth, TexasSAE Aero Design West 2024 (Advanced Class): 1st place Design Report and 5th overall
Location: Los Angeles, California
AEAC 2024: 3rd place in Phase 1 Design Paper
Location: Alma, QuebecAEAC 2023: 2nd place in Phase 1 Design Paper
Location: Alma, QuebecUSC 2022: UTAT UAS, Judges Award
Location: Southport, MBUSC 2021: UTAT UAS, 1st place in Phase 1 Design Paper, 2nd place in Phase 2 Airborne Flight
Location: Virtual
Notable achievements of the ancestral teams of UTAT UAS
USC 2017: UTAT UAV, 1st Place in flight portion
USC 2016: UTAT UAV, 1st place in design
AUVSI Student UAS Competition 2015: UTAT UAV, 2nd place in mission and 5th overall
USC 2015: UTAT UAV, 2nd place in design phase
USC 2014: UTAT UAV/AeRo, 1st/2nd place in design phase
AUVSI Student UAS Competition 2013: UTAT UAV, Best Oral Brief
USC 2013: UTAT UAV, 2nd place in operational phase and design phase
SAE Aero Design West 2014: UTAT Powered Flight, 2nd place in oral presentation, and 3rd overall
SAE Aero Design East 2013 (Micro Class): UTAT Powered Flight, 2nd place in oral presentation and 4th overall
SAE Aero Design West 2012 (Advanced Class): UTAT Powered Flight, 2nd place in design, 3rd in oral presentation, 2nd place in best DAS accuracy, and 2nd overall
SAE Aero Design West 2012 (Micro Class): UTAT Powered Flight, 1st place in oral presentation and 2nd overall
SAE Aero Design West 2012: UTAT Powered Flight, NASA System Engineering Award
SAE Aero Design West 2011 (Regular Class): UTAT Powered Flight, 1st place in design
Team Leadership
-
Jeffrey Zhao
UAS Director
-
Joey Zou
AEAC Chief Engineer
-
Sencer Aksu
SAE Chief Systems Engineer and Project Manager
-
Kai Chen
SAE Chief Airframe Engineer
-
Thomas Hafner
AEAC Electrical Co-Lead
-
Tommy Zhang
AEAC Electrical Co-Lead
-
Oliver Harrison
AEAC Mechanical Lead
-
Di Hu
AEAC Flight Dynamics Lead
-
Benjamin Low
AEAC Software Lead
-
Frank Yan
SAE Structures Lead
-
Kevin Wang
SAE Electrical Lead
-
Yume Yamamoto
SAE Software Lead
-
Michael Law
SAE Aerodynamics Lead
Unmanned Aerial Systems Portfolios
-
Yang Niu
Business Development Lead
-
Yume Yamamoto
Outreach Lead
-
Alex Qin
Brand & Media Lead
-
Krrish Sharma
Organizational Development Lead